Have you recently encountered the term SMED but are uncertain of what it means? In this article, we will help you discover what SMED is, what it entails, its benefits, and how to implement it in your firm or organization. Keep reading to find out.
What is Single-Minute Exchange of Die? (SMED)
Single-Minute Exchange of Die (SMED) is a lean production process that significantly reduces equipment setup time. Equipment changeover involves the time it takes to convert the manufacturing process from making one product to the next.
SMED is a quick and efficient method of streamlining operational processes. Reducing equipment startup time results in less waste and reduces lead times.
The expression "Single-Minute" can be quite confusing since the startup time does not take one minute to complete. Instead, the phrase means that the changeover takes less than 10 minutes or single-digit minutes to complete. For instance, the process can take 4, 5, or 6 minutes to complete.
Die refers to a tool used in manufacturing to produce specific material forms and shapes in succession. Not only can you apply SMED in manufacturing processes, but also in other aspects like organizational management, software development, etc.
Explore the SMED Method in a simulated Manufacturing environment!
The best method to explain SMED Method to your employees, students on a real case study!
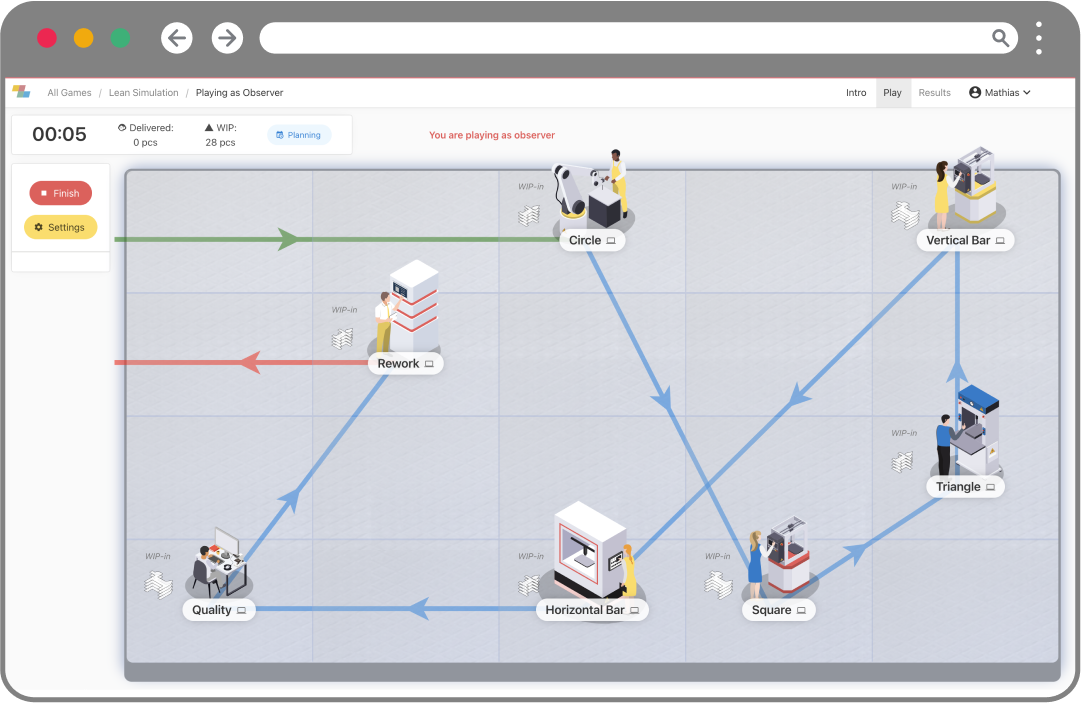
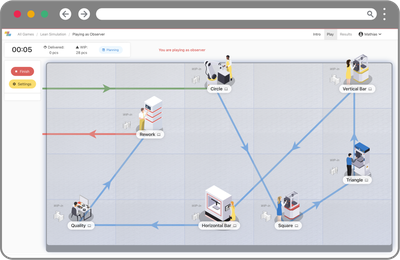
When was Single-Minute Exchange of Die invented?
Single-Minute Exchange of Die (SMED) first came into light as Quick Die Change (QDC) in 1955 when Taiichi Ohno improved the changeover time for Toyota presses.
With time, Toyota made improvements to its production process. The company reduced the changeover time from hours to 180 seconds by the 1990s.
Shigeo Shingo officially developed the term SMED when he changed Quick Die Change to Single-Minute Exchange of Die in the 1970s. He relocated to the US and engaged in lean manufacturing consultation.
Shigeo promoted SMED in the US where the solution continued to gain traction. Since its implementation, SMED has resulted in about 94% reduced changeover time in numerous industries.
How does SMED work in practice?
SMED reduces startup time by streamlining external and internal elements. External elements occur when the manufacturing process is still running, while internal activities happen when the process stops. Internal and external elements are crucial for implementing SMED.
External activities simplify internal processes required to complete a process. Setting up external elements in advance reduces time wasted in completing a process.
For instance, in racing, pit crews gather the necessary tools needed to streamline the car racing process. If the crew begins to look for tires when the car stops, a lot of time is wasted. Similarly, a chef in a restaurant gathers all materials necessary to prepare lunch or dinner before the actual time reaches.
The goal is to convert as many internal steps as possible into external steps. Companies and organizations need to analyze what materials and tools they need to complete operational processes beforehand.
A perfect example of SMED in action is when Toyota reduced equipment setup from around 8 hours to 3 minutes in the 1990s. The company simplified the process by eliminating unnecessary procedures and simplifying the operational process.
How do you implement SMED?
Implementing SMED requires careful consideration and analysis. Here is how you implement SMED in manufacturing, supply chain, management, and other work functions.
Identify the problem
The first step is identifying why you are losing time and where you can make improvements. Note what is causing delays in your workplace operations. Identify areas with the longest setup processes and those with varying changeover times. Look for areas where changeover occurs frequently.
Take note of internal and external elements
Identify external and internal components required to complete a process. What tools are required for external setup? How often does the process need internal and external components? Take note of how long it takes to complete specific tasks.
Separate external elements from internal ones
Can this step take place when the production process is still running? If so, mark the process as external. Identifying external processes allows organizations to accomplish some tasks before the changeover is complete.
For instance, gathering materials and tools needed for the next step reduces time wasted and improves operations.
Convert internal setup to external elements
Look out for any internal steps that you can convert into external components. Are there parts of machines you can clean while the process is running? Can you prepare materials in advance?
Converting internal elements into external ones improves efficiency and reduces costs and waste. Converting internal activities also reduces lead times and maximizes productivity.
Streamline operations
Can you simplify work operations? If so, what tasks will you focus on? Modifying equipment to reduce startup time is one way to streamline operations. You can also opt to replace a tool or equipment with a better one that reduces lead times, maximizes productivity, and minimizes waste.
Train your team
Implementing SMED requires you to change different aspects of business operations. This means training the team members to adopt the new procedures. They need to know how the new process will affect various contexts of working operations.
You can also show them how the new procedures will improve efficiency. This way, they will be more willing to implement the new process. Set new policies that your team can follow. These new policies will act as the team's goals.
Repeat the process
Implementing SMED is a gradual process that requires practice. You might not complete the setup within the desired timeline during your first implementation. To achieve the single-digit-minute startup, you will need to repeat the process several times.
The best tool to explain SMED implementation! Used by:
-
Lean Managers, Production or Operations Directors
Six Sigma Black Belts, Green Belts, Continuous Improvement Coaches
- Training Managers, Management Consultants
- Operational Excellence.
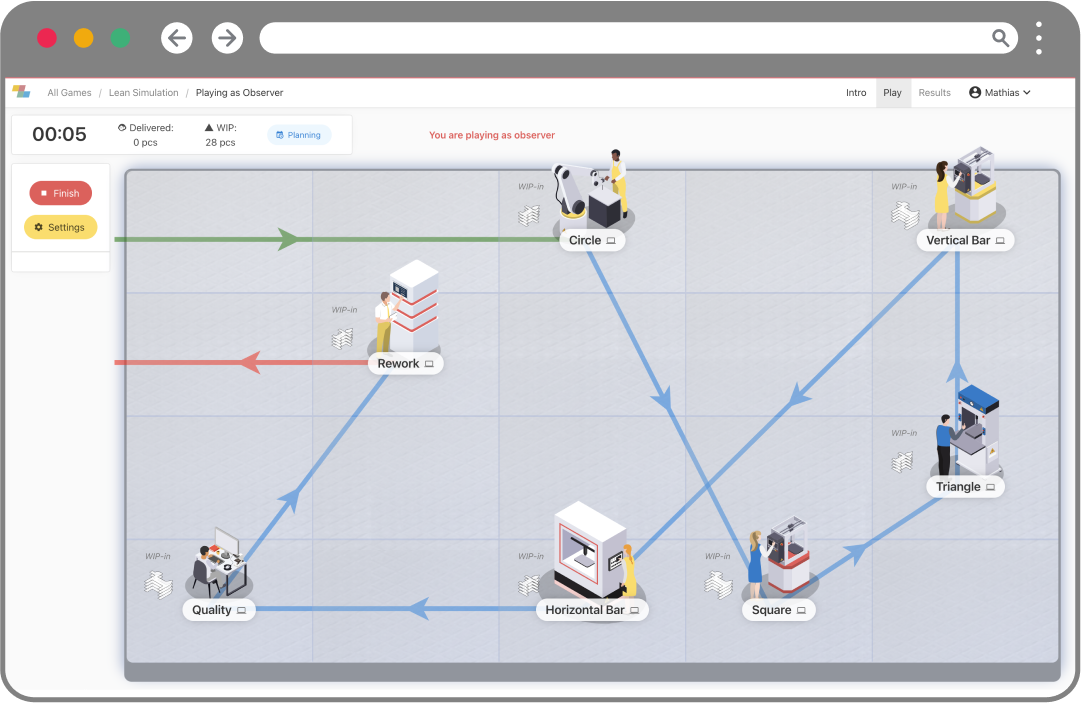
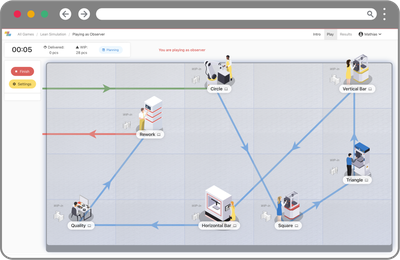
What are the benefits of implementing SMED in a production process?
Implementing SMED has several advantages, including:
Reduced manufacturing costs
SMED ensures quick setup that, in turn, results in reduced lead time and equipment downtime. When processes run continuously, organizations can cut down operational costs significantly.
Diversified product types
Implementing SMED allows organizations to diversify products. This lean method allows firms to switch from one product to another without compromising quality. SMED also reduces the time it takes to switch from producing one product to the next.
Increased productivity
Implementing SMED increases productivity by streamlining operational processes. SMED eliminates bottlenecks that slow down processes. With reduced delays, companies can maximize productivity and maximize ROI.
Improved quality
Companies can improve the quality of their products and services by implementing SMED. The shorter setup time leads to creating quality products and services. This lean process also allows firms to deliver products and services to customers on time and within budget.
Enhanced safety
Implementing SMED allows organizations to identify unsafe processes and make improvements to enhance safety. Companies can implement safe procedures and enhance workplace safety.
Smaller batches
SMED promotes smaller batches. Smaller batches, in turn, reduce inventory and material handling. Organizations also free up warehouse space needed for inventory through this lean manufacturing method.
Smaller lot sizes produce less waste which promotes sustainability. When employees are not handling inventory, they can focus on addressing customer needs and boosting productivity.
Improved Customer satisfaction
By implementing SMED, organizations can respond promptly to customer demand. This solution allows firms to schedule production and distribution more easily and on time. When customers are satisfied, they are likely to return for more services. More customers could lead to more profits and a higher ROI.
Reduced defects
SMED allows firms to minimize defects in their work process. By streamlining operations, there are fewer adjustments needed to produce quality products. SMED also promotes the production of smaller batches resulting in fewer defects.
Minimal waste
Since business processes are quicker when using SMED, there is minimal waste. Organizations can manage inventory and reduce material deterioration. Inventory also moves fast when production is consistent and fast.
Reduced production time
SMED simplifies processes and reduces machine downtime period. When there are fewer interruptions, the process becomes quicker. Organizations can produce more products within a shorter time frame.
Zensimu's lean game
Zensimu's Lean Game allows participants to learn how SMED works through a simulated workshop. Through this game, professionals can train employees or students to implement SMED in different contexts to achieve better performance.
This tool provides a lens into the real world, where SMED streamlines processes and maximizes efficiency. Using Zensimu, professionals provide helpful insights to their employees that they can use to streamline work processes.
Teachers also help their students learn how they can implement SMED in the real world to drive positive impact. The game shows how SMED improves machine flexibility resulting in more improvements like:
Diverse and high-quality products
Reduced material handling
Flexible work stations
Smaller batches
Increased reactivity
Zensimu allows professionals to drive SMED concepts more clearly and help trainees grasp ideas more easily. This game allows firms to build teamwork, enhance efficiency, and boost productivity in the long run.
Explore the SMED Method in a simulated Manufacturing environment!
The best method to explain SMED Method during training programs, onboarding program, team-building, client kick-off, seminars, workshops!
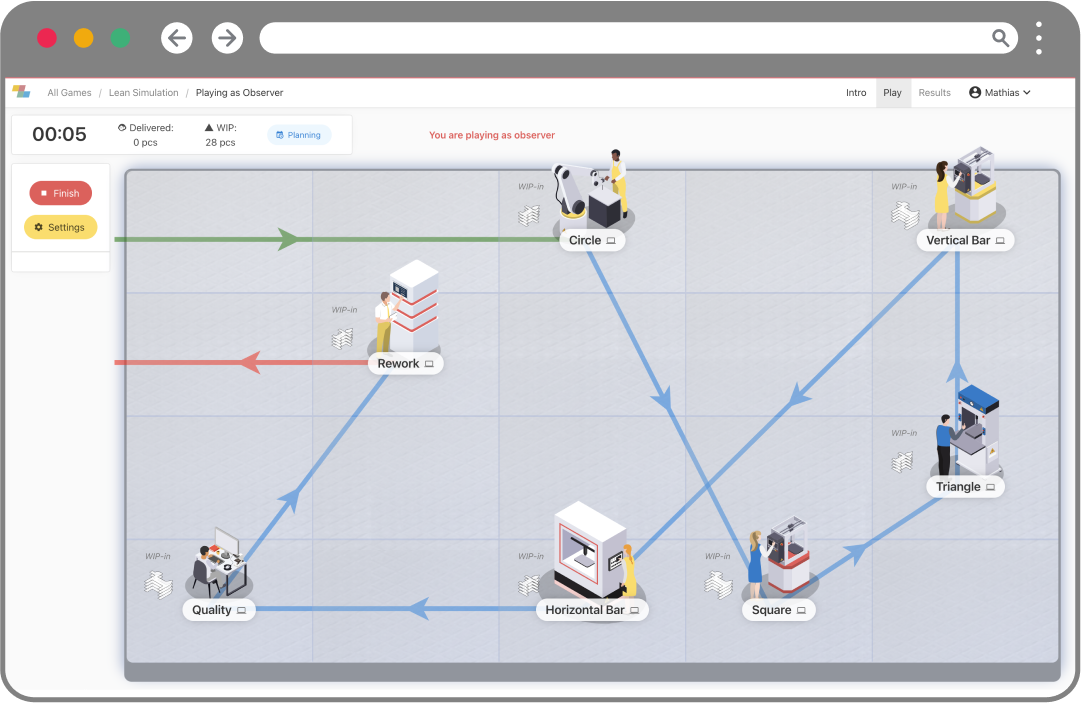
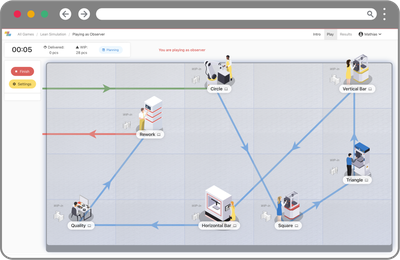
Bottom line
SMED is a sustainable solution that helps organizations streamline processes and maximize efficiency in the long haul. SMED implementation involves several considerations pertaining to your organization's needs.
Companies reap several benefits by integrating SMED into various operational aspects. For more information, feel free to contact us today.