What is Lean Manufacturing?
Inspired by the Toyota Production System, developed by the automotive company in the 20th century and referred to as “just-in-time production”, Lean Manufacturing is a method of production aimed at increasing efficiency by reducing time within the system as well as response times from suppliers and customers.
According to the book The Machine That Changed The World—written by James P. Womack, Daniel T. Jones, and Daniel Roos—there are five main principles to Lean Manufacturing:
Defining value: where market research is conducted using qualitative and quantitative techniques and studies to determine what products or services customers would demand, how they want it produced and delivered, and how much they are willing to pay for said products or services.
Mapping the value stream: where types of waste is eliminated from the production process so that customers receive exactly what they want and the manufacturer reduces costs by not wasting resources on unnecessary steps or production aspects that do not add value to the end product.
Creating flow: where all the remaining production steps are optimized to run smoothly without delays or interruptions once waste is removed in the previous step.
Using a pull system: where inventory and work-in-process (WIP) items are limited ensuring that products are manufactured exactly at the right time and quantities with the demands of the end customer in mind.
Pursuing perfection: where company employees constantly seek lean and continuous improvements throughout the production process, establishing an organizational culture of daily learning.
Explore the Lean Manufacturing benefits in a simulated environment!
The best method to explore Lean Manufacturing with your employees, students on a real case study!
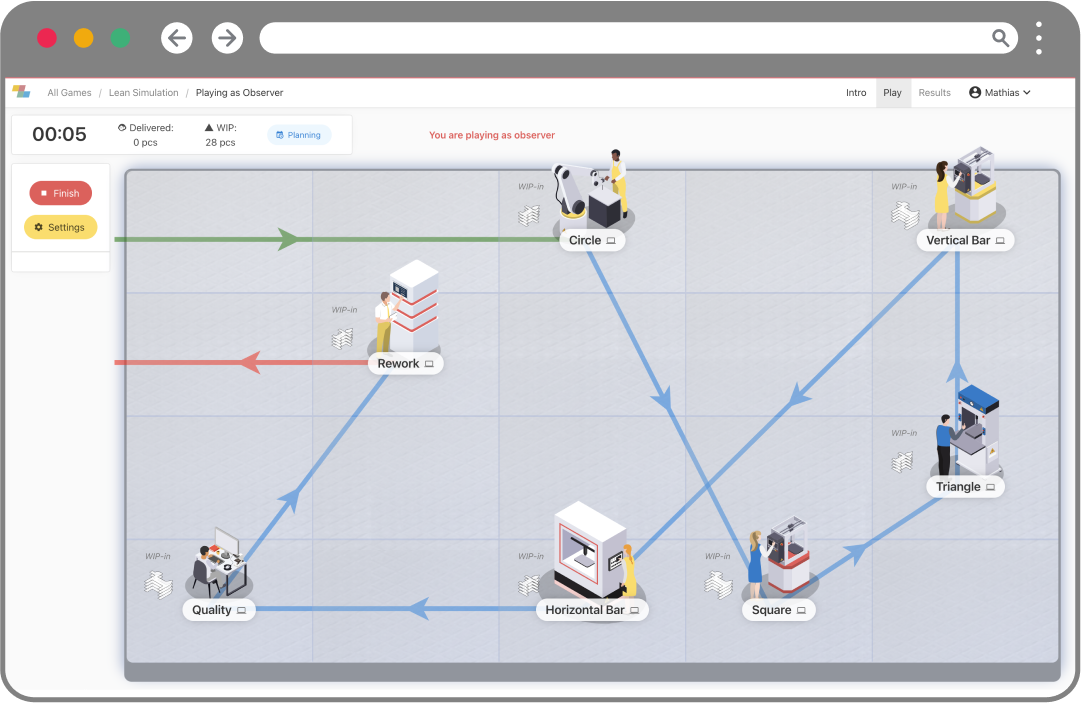
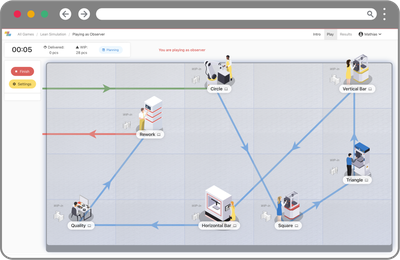
How is Lean Manufacturing revolutionizing the industry?
Lean Manufacturing has greatly evolved production processes all over the world by reducing capital needed to achieve a given output and/or sales objective in order to increase overall profit. Specialized lean tools have even been developed to help companies focus on the most important production factors as well as identifying and reducing waste.
Within the Lean Manufacturing framework, here are seven main types of waste. If you put together the first letter of each waste, it forms the common name "TIMWOOD":
Transportation waste: The unnecessary movement of parts between workstations and/or factories and warehouses where the distance between steps can be reduced.
Inventory waste: Having more than the required stock for maintaining a continuous production flow.
Motion waste: The unnecessary movements and travels of operators, such as retrieving tools, parts, documents, etc.
Waiting waste: This occurs when operators rest idle during a machine cycle, waiting for parts, essential information or equipment maintenance.
Over-Processing waste: This is the unnecessary or incorrect work on a part compared to customer requirements, either due to defective machines or a bad product design.
Overproduction waste: This occurs in the production process when too many parts are produced or produced too early compared to customer requirements.
Defect waste: This is time lost when needing to inspect, fix or scrap defective parts.
How can Zensimu help you with Lean Manufacturing teaching?
Companies serious about incorporating a Lean Manufacturing framework into their operation teams must not only familiarize employees with its theories, but provide practical exercises to see how concepts, such as operational excellence, waste avoidance, defect removal, etc., actually work on the ground.
Zensimu’s Lean Game simulates real-life scenarios in which the five Lean Manufacturing principles—identifying value, mapping the stream, creating flow, adding pull, pursuing perfection—can be applied. By playing several rounds at the start of a company’s Lean implementation program, participants will have a particularly clearer understanding of the agenda and objectives.
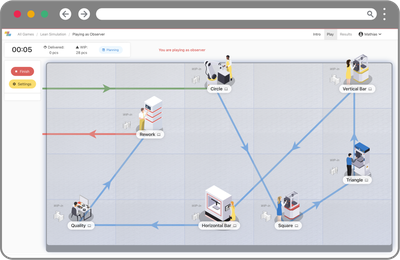
The Lean Game is a fun way for players to see how to remove or decrease buffers in the production process, how failures can have major impact, and why adhering to true Lean principles requires a change within the culture of the organization.
Ultimately, the Lean Game provides players a sense of satisfaction in seeing how smooth a production process can become, which also positively reflects on the bottom line.
The best tool to explore Lean Manufacturing! Used by:
-
Lean Managers, Production or Operations Directors
Six Sigma Black Belts, Green Belts, Continuous Improvement Coaches
- Training Managers, Management Consultants
- Operational Excellence.
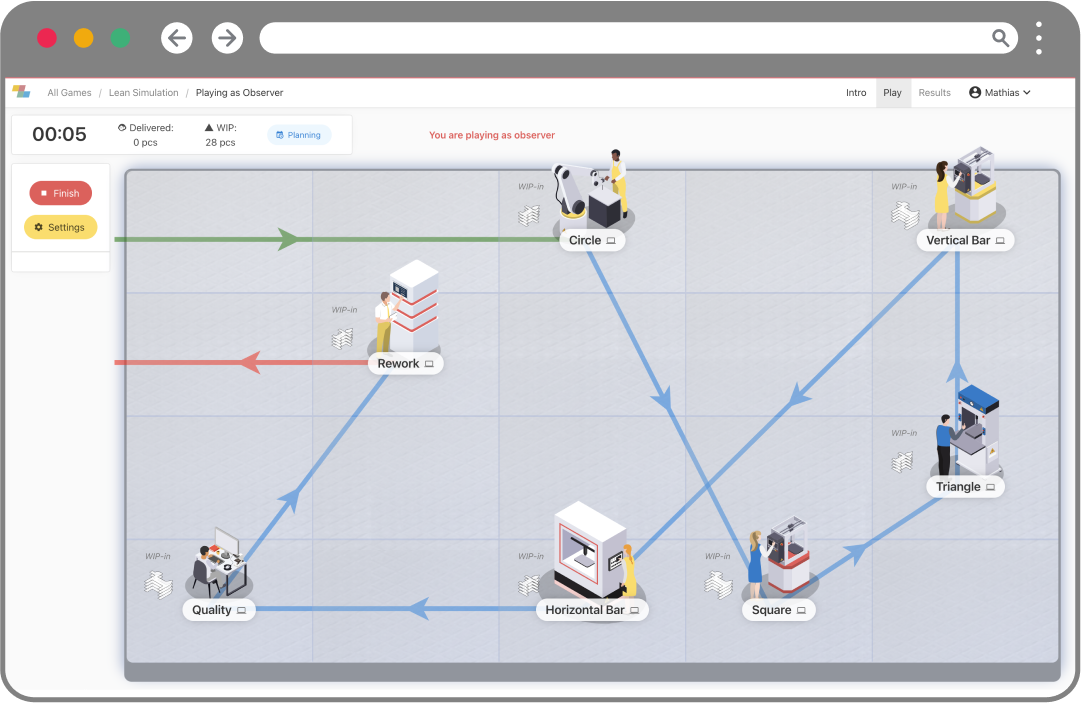
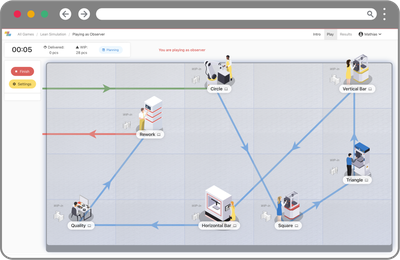