If you are planning to lower the costs of production of your company by reducing the time wasted between production processes and eliminating unnecessary waste, then you need to implement the Kanban approach. It will help to reduce lead time and minimize your inventory. Here is everything you need to learn about the approach.
What is Kanban?
It is a Japanese term that means billboard or signboard and is used in the scheduling system of lean manufacturing. Kanban, also known as the visual card system, was developed by Taiichi Ohno, an industrial engineer at Toyota to help improve the efficiency of the manufacturing processes.
The original visual card system used by Toyota involved the use of visual cards which were handed out in each department as a means of communication between the departments. As technology evolved, companies started using virtual boards to communicate with employees. Today, industries manage the visual card system digitally to provide open and transparent communication in projects.
Explore Kanban method in a simulated Manufacturing environment!
The best method to explain Kanban Method in manufacturing to your employees, students!
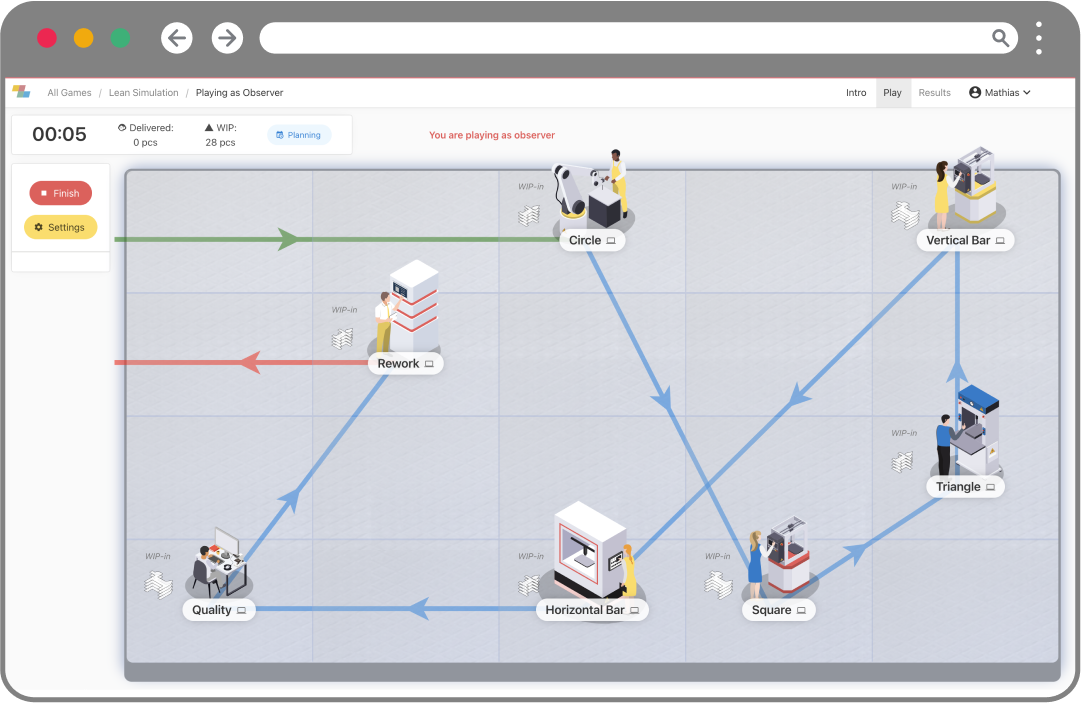
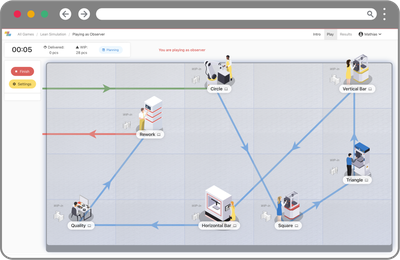
How do you implement the approach in practice?
If you want to implement the visual card system in your company to reduce the lead time and increase production, you need to use the following approaches:
Create optimal conditions
You can implement the visual card system successfully in your manufacturing processes by creating an optimal environment. If you do not provide the ideal conditions for the system, it will be hard to implement and will require you to have a larger safety margin. Some of the most optimal conditions for implementing the visual card approach successfully in manufacturing include:
Ensure you have a stable predictable product demand
Make certain the production system follows a specific flow for all work processes
Ensure you have few variations of products and use machines that are smaller in size
Use SMED (Single Minute Exchange of Die) techniques
Use production processes that are repeatable
Failure to fulfill the above conditions may cause you to spend more time analyzing the work processes in order to create the best visual card system.
Set up a pull production system
Since the visual card system is part of lean manufacturing, it also belongs to the pull system, which controls what is produced by an organization, how much is produced, and when it is produced. The purpose of the pull system is to make certain that your company produces only what customers demand without exceeding the amount of demand. Therefore, in order to implement the visual card system and set up pull production, you need to observe the following rules:
Never pass defective products to the next production process
Always ensure production is leveled
Produce according to demand and do not exceed
Ensure the production process is stable and rational
Different types of visual card systems
Once you successfully create optimal conditions for the visual card system, you can use any one or more of the following approach methods:
Using cards or bins at each step of the process
The card approach refers to the use of cards attached to batch materials as they move to the next production flow. Most of the times, about two or three cards are used for each product in the system. Bulky products or larger batches may have more than three cards attached to them. The cards on each product contain important information about the product e.g. what the product is, where to use the product in the production flow, and the quantity of the product required.
Depending on the production processes of your company, you can use a two card system or a multiple card system.
The two card system
In this process, when a step in the production system is completed using materials that had a specific visual card attached, the card is returned to the prior step where it is used as an authority signal for the previous production step in order to produce replacement steps.
The multiple card system
For this process, the prior stage of production waits for a specific number of cards to return before the manufacturing of more products continues.
Bins are used in a similar manner to the cards in the production process. However, instead of attaching cards to the materials, the bins that store the materials are used as Kanban. This means that the bins are returned to the previous production process after they are emptied to send a signal to restock and produce more products. Moreover, the bins are labeled with important information about the products, just like the cards. However, unlike cards, the bins are used for one type of material only.
CONWIP
CONWIP stands for continual work in progress and is an approach that resembles the method used to restock shelves in supermarkets. In this case, the Kanban is the location of the product e.g. the floor space or empty shelf. The production schedule of the CONWIP system depends on the demand of the product. The CONWIP method is favored more by manufacturers compared to the bin system because it has a higher lead time and helps manufacturers to decrease their inventory level.
E-ban
Thanks to modern technology, companies can set up a digital paperless system to pass important information during production processes. Bar code scanners are excellent because they are able to pass information about products via electronic messaging.
E-ban systems are more effective than bins and cards because they communicate at a higher speed, thereby speeding up the production process to ensure that the products are manufactured on schedule.
The best tool to explain Kanban implementation! Used by:
-
Lean Managers, Production or Operations Directors
Six Sigma Black Belts, Green Belts, Continuous Improvement Coaches
- Training Managers, Management Consultants
- Operational Excellence.
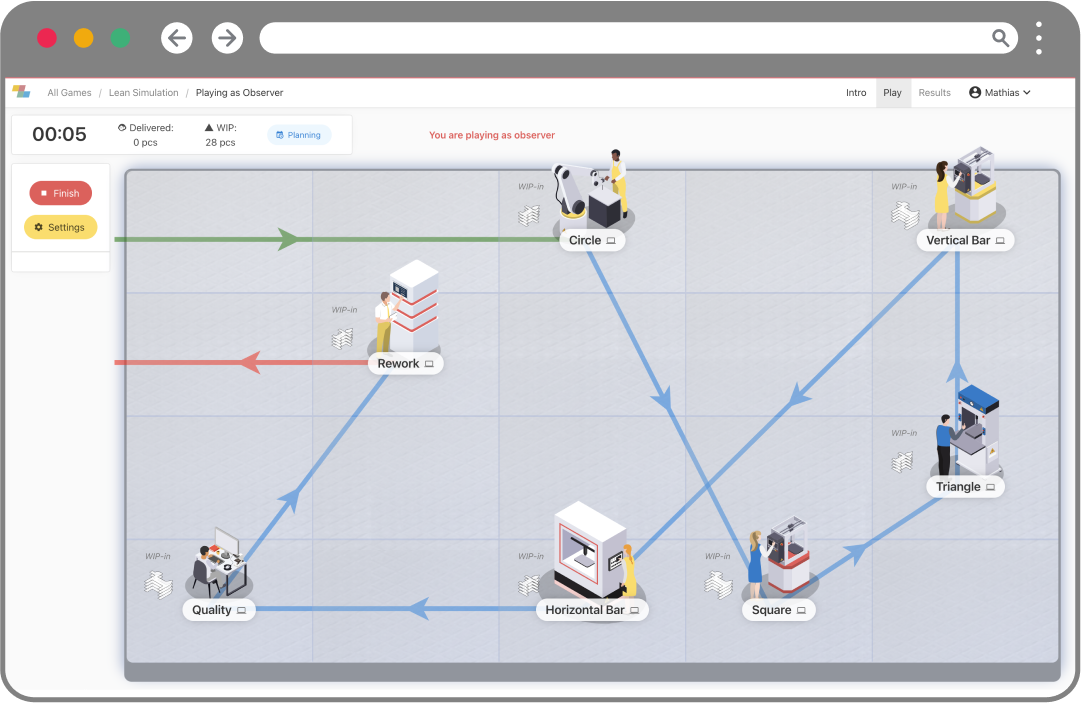
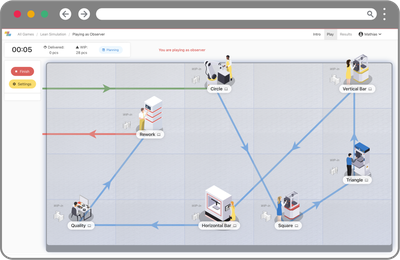
Why do we use the visual card system?
The visual card system is beneficial to companies because it helps to visualize the production process making it easy to understand. Additionally, the approach helps to cut costs of production by optimizing the production procedures and reducing time and material wastage. The visual card approach also helps to optimize the inventory methods by minimizing the inventory to eliminate overproduction and reduce waste.
Companies that have managed to reduce their work-in-progress stock and managed to significantly reduce the lead time using the visual card approach include:
Nike- successfully implemented the approach to improve poor working conditions by standardizing demand for their products through canceling late orders and reducing waste.
Jaguar- improved their performance by cutting their delivery time, reducing batch sizes, and improving the quality of their products.
Spotify- when the company was struggling to schedule and manage planned projects, they used the visual card system to split the big projects into manageable parts for better planning and organization.
Pixar- implemented the approach to produce 3D animation, which ensures that every Pixar production is manufactured.
Zara- being the largest fashion retailer, it implemented the visual card approach to ensure its stores hold just-in-time inventory to deliver products according to demand level.
Seattle Children's hospital-due to problems with inventory of hospital supplies and wastage of time by hospital staff, the hospital used the two-bin system to determine optimal stock levels so that the hospital never runs out of supplies.
In software agile development, the visual card approach is used as a helpful technique to limit the workload of the software developers and make sure all the IT projects are handled faster from start to finish, thereby reducing the work-in-progress to reduce the lead time.
Get started with Zensimu today
If you are planning to implement the Kanban approach in your company, then Zensimu bring the training tools needed for your team. We will provide our lean game system to train your employees about the visual card system approach in a simulated workshop so that they can get first-hand experience of how the communication technique works.
We also offer a deeper level of Kanban training whereby we set up materials at each station based on their cycle time to allow participants to understand better how the visual card approach works.
Explore the Kanban Method in a simulated Manufacturing environment!
The best method to explain Kanban Method during training programs, onboarding program, team-building, client kick-off, seminars, workshops!
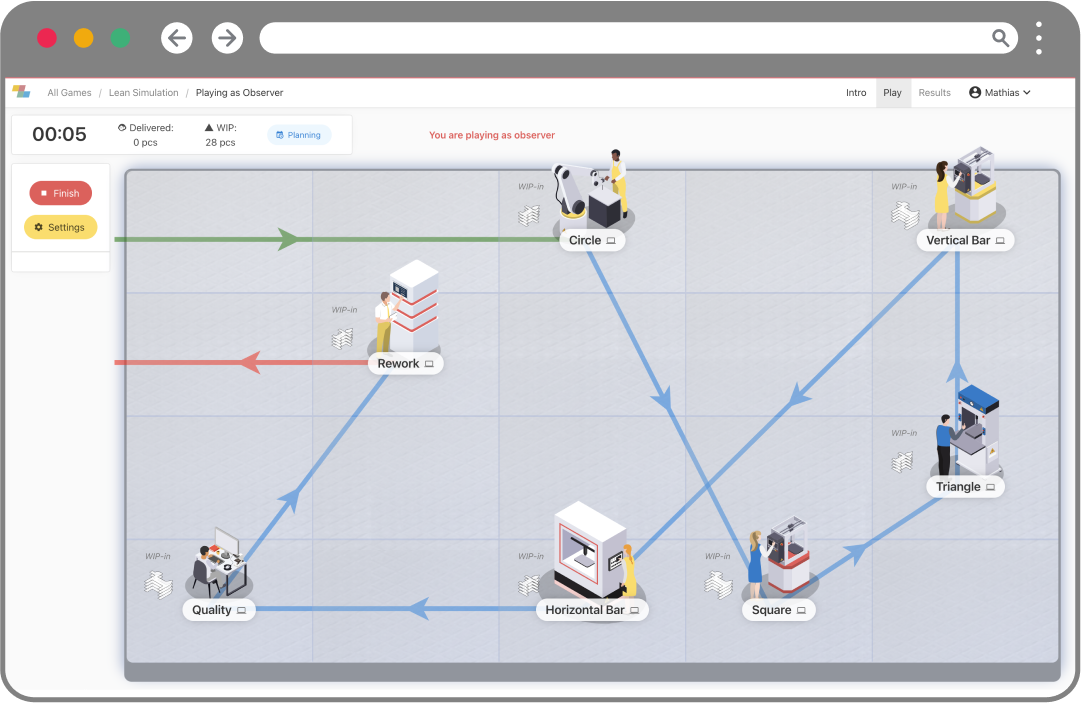
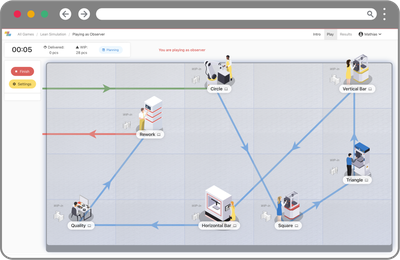