The Six Sigma technique is a business methodology that aims towards quality improvements in organizations by identifying the number of defects in the business processes and finding ways to eliminate them.
The Six Sigma process was developed in the 1980s by an engineer who worked for Motorola called Mr. Bill Smith. Bill Smith created the Lean Six Sigma management system that led to a reduction in the number of variations in the electronic manufacturing procedure at Motorola. His discovery led to a decrease in the number of product defects, and so the methodology was called the Lean Six Sigma system.
Over time, project teams and company leaders in different industries adopted the strategies and tools of the lean management system to:
Increase their productivity, and drive up their profits
While decreasing the cost of production and minimizing waste.
The Six Sigma technique is effective because it utilizes the data and statistics of an entire organization to eliminate errors. By using factual information about an organization, the Six Sigma method is able to transform business processes and attain better quality control.
Explore the Six Sigma method in a simulated Manufacturing environment!
The best method to explain Six Sigma method to your employees, students on a real case study!
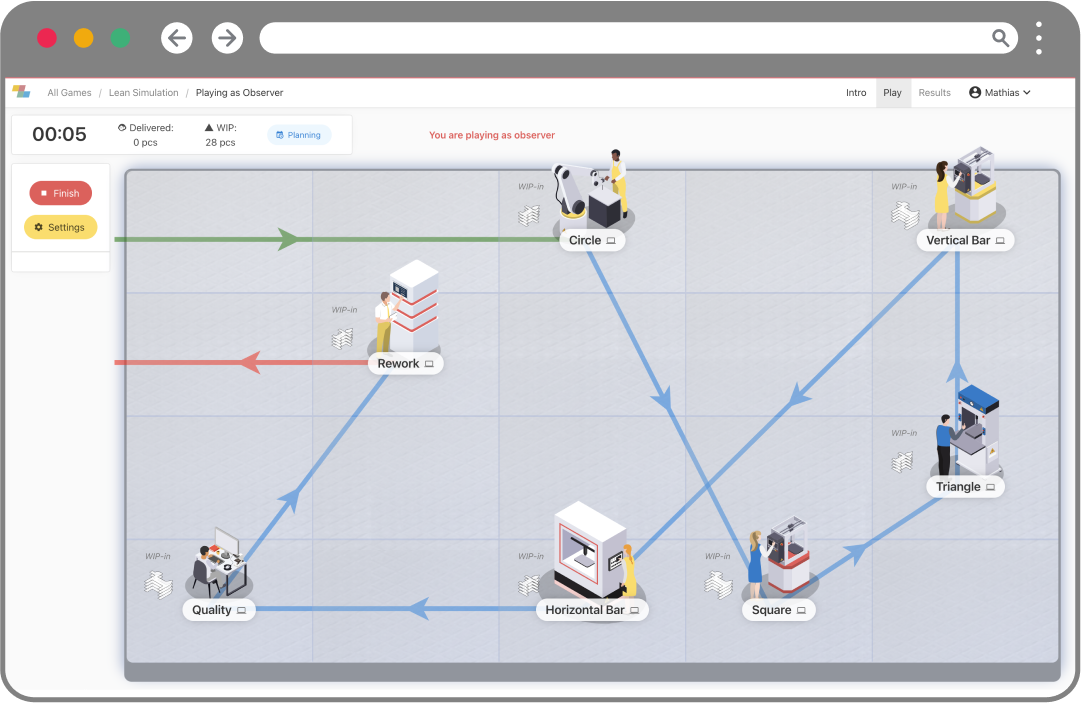
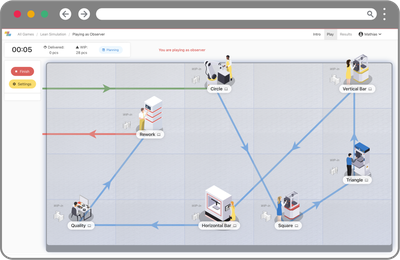
In order for the Six Sigma managerial technique to be effective in helping your business deliver excellent products and services to achieve maximum customer satisfaction, you need to observe the following key principles:
Prioritize the customer
This key principle is based on the fact that the customer/client is the king of your business. Therefore, your main goal should be to ensure that the customer derives the most benefit from your product or service. This shows that you need to understand the needs of your customers, why they purchase, and what motivates their loyalty to your brand.
In addition, you need to establish the quality standard of your products or services based on the market demand.
Measure value and identify the problem
Gather detailed information on the various business processes in your organization to identify the areas that generate waste instead of output. To spot the areas of waste successfully using the Six Sigma method, ensure that you have specific data collection goals. Among the goals to specify include:
Defining all the collected data
Identifying the reason for gathering data
Outlining the expected insights
Making certain the measurements are accurate
Creating a standardized system of data collection
Once you collect the data, analyze whether it needs to be refined or not, and whether it is helping your company achieve its targets.
Remove the waste
After identifying the source of problems in your business processes, take action to make changes in the procedures to remove the occurrence of defects. For instance, you can eliminate all the activities that do not work towards increasing customer satisfaction and value.
Bring in the stake holders
In order to minimize the risks and produce optimal performance, you need to come up with a structured process, in which all members of your team can contribute their opinions to help solve problems in the production procedures.
Create a flexible ecosystem
The main aim of the Six Sigma method is to promote change and transformation in organizations. In order for the inefficient methods to be removed to reduce waste, change needs to be implemented in various procedures and employee approaches.
By creating a flexible and responsive ecosystem within your organization, your employees will be able to adapt easily to the change.
Explore the Six Sigma method in a simulated Manufacturing environment!
The best method to explain Six Sigma method to your employees, students on a real case study!
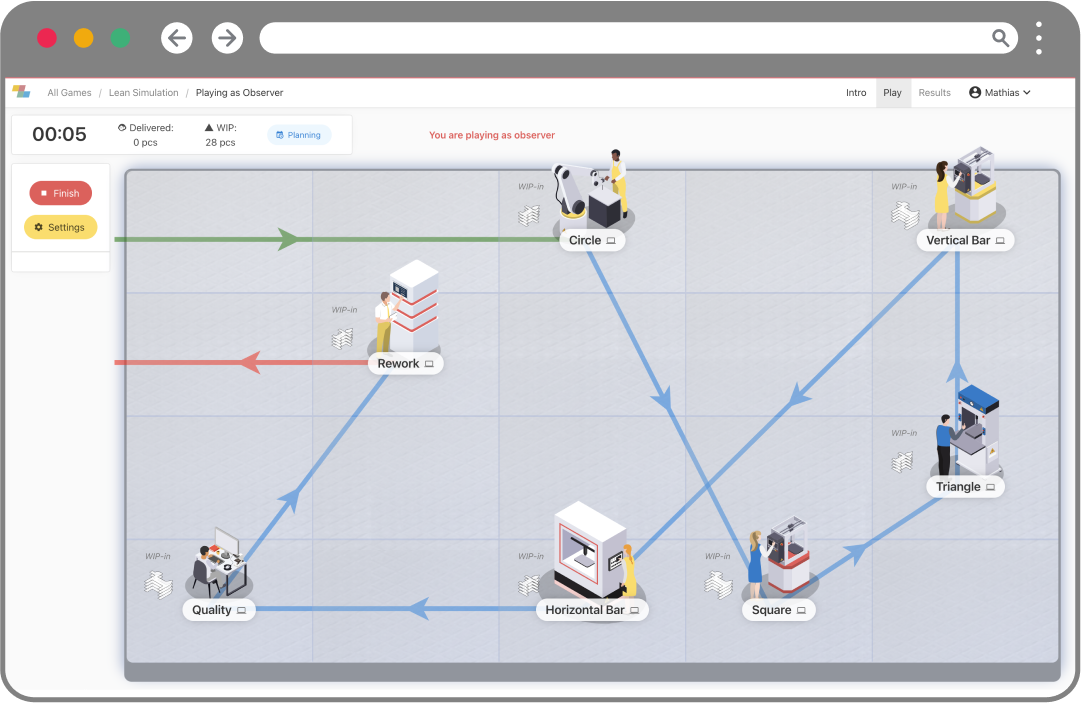
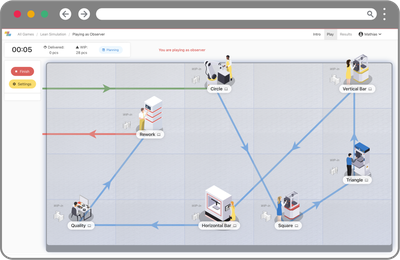
How Does the Six Sigma Approach Work?
Six Sigma is mainly used for statistical quality control in organizations. Back in the 1920s, Walter Shewhart, a pioneer in Statistical Process Control, discovered that three sigma deviations from the mean in lean manufacturing is the specific point that indicates the manufacturing procedure has too many defects. Any manufacturing procedure that had more than three sigma deviation from the mean needed to be improved immediately to minimize waste.
For many years, this was the norm of standard quality in manufacturing and production industries until Bill Smith came up with a new theory, the Six Sigma technique. After gathering and analyzing data more keenly, Bill Smith proposed that Six Sigma was the point of deviation from the mean that indicated a procedure needs to be changed to reduce wastage.
Bill Smith further argued that it was impossible to attain zero defects in Statistical Process Control, thereby making Six Sigma a more reliable measurement standard. Moreover, three sigma allows about 66,807 defects for every million production opportunities while six sigma allows only 3.4 defects for every one million opportunities (0.00034%).
Although Six Sigma is considered the most optimal of all measurement standards, there are companies that reach 3 or 4 sigma and are still sufficient in production.
Six-sigma Methodology for Improvement Projects: DMAIC
DMAIC is a five-step breakdown of the Six Sigma method, which aims to improve the outcome of projects in organizations. It consists of the following:
Step 1: Define
In this step, the company identifies all its goals as well as its customer deliverables.
Step 2: Measure
The company leaders measure the product capabilities as well as important components of each work method.
Step 3: Analyze
In this stage, the data collected is analyzed to determine the root cause of any issues and defects in the procedures.
Step 4: Improve
The company establishes procedures to remove the defects from the business processes to increase output.
Step 5: Control
Here, the team leaders come up with methods to control how the process will be carried out in the future.
Another Six Sigma methodology is DMADV, which also has five stages that consist of the following:
Define
Measure
Analyze
Design
Validate
The DMADV methodology is applied when the current procedures in an organization do not meet customer requirements even after the production method has been optimized. In such cases, the DMAV methodology is executed by the following types of Six Sigma:
Green Belt Six Sigma
- a certified Lean Six Sigma expert that leads improvement projects.
Black Belt Six Sigma
- a certified Six Sigma professional tasked with providing expert leadership.
Yellow Belt Six Sigma
- a certified Six Sigma PDCA (Plan-Do-Act-Check) expert that identifies procedures that need improvement.
Explore the Six Sigma method in a simulated Manufacturing environment!
The best method to explain Six Sigma method to your employees, students on a real case study!
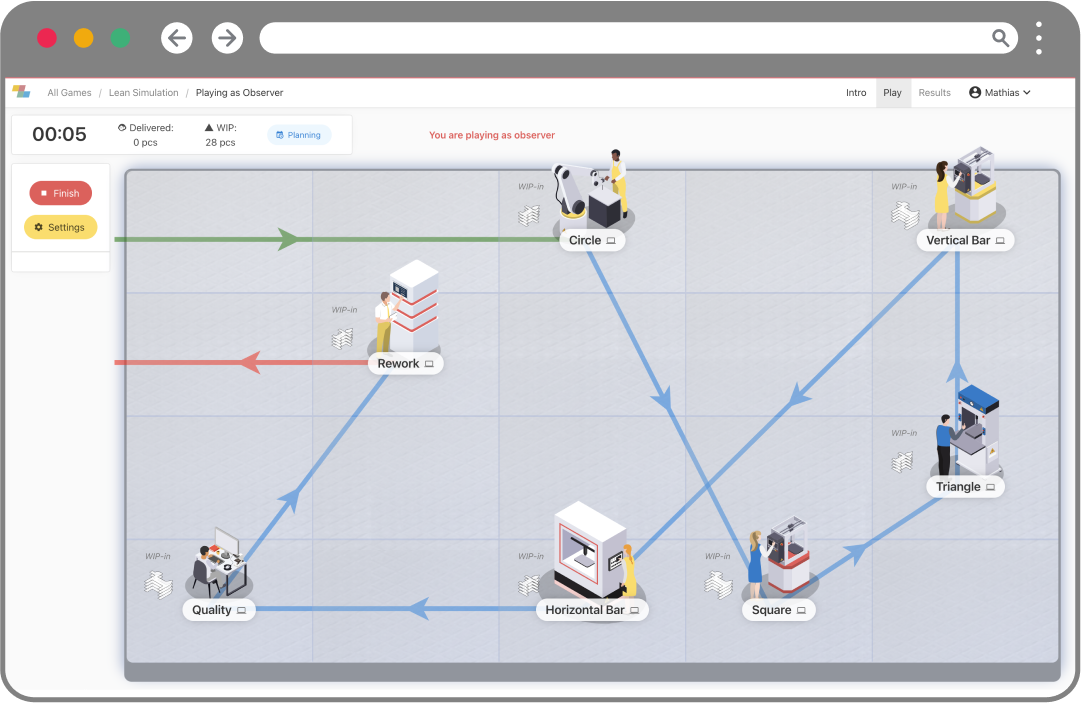
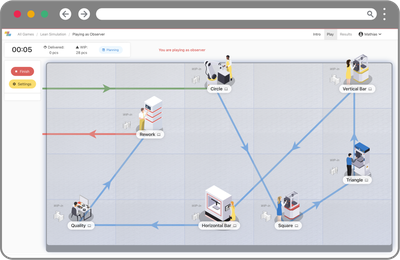
What are the benefits of Six Sigma?
Here are the various ways that the Six Sigma approach will benefit your organization:
A decrease in waste
The main aim of the Six Sigma approach is to help your company optimize its production procedures and minimize wastage. Once you identify the areas within your organization that contribute the highest percentage of wastage, you can save more money and resources by eliminating all the wasteful procedures.
An increase in efficiency
When you reduce waste in your business processes, your organization records a higher output every time it utilizes more resources. This reflects an enhanced efficiency and productivity of your organization.
A decrease in errors
In addition to paying attention to business processes, the Six Sigma approach also prioritizes the quality of output. By reducing the number of errors, your company will produce better-quality products and services.
Get Started with Zensimu Today
If you want to successfully implement the Six Sigma approach in your organization, then you need to train your employees properly in order to increase their efficiency and eliminate all areas of wastage. Luckily for you, you do not need to spend hundreds of hours training your team.
At Zensimu, we use a lean game technique that allows all participants to identify opportunities for improvement in a production procedure. This will allow your employees to follow up on data results and adapt the Six Sigma methods more quickly by learning them in a risk-free environment.
The best part is that our games are easy to learn and simple to navigate, which will allow your employees to understand the Six Sigma concept better because they will practice by doing. Investing in training your employees using our games is a smart business move because they will practice in a risk-free environment that gives them room for error until they fully understand the Six Sigma process before you officially implement it in your organization.
Explore Six Sigma the Six Sigma benefits in a simulated Manufacturing environment!
Your employees or students can now apply the theoretical principles of the Six Sigma technique on a real case study!
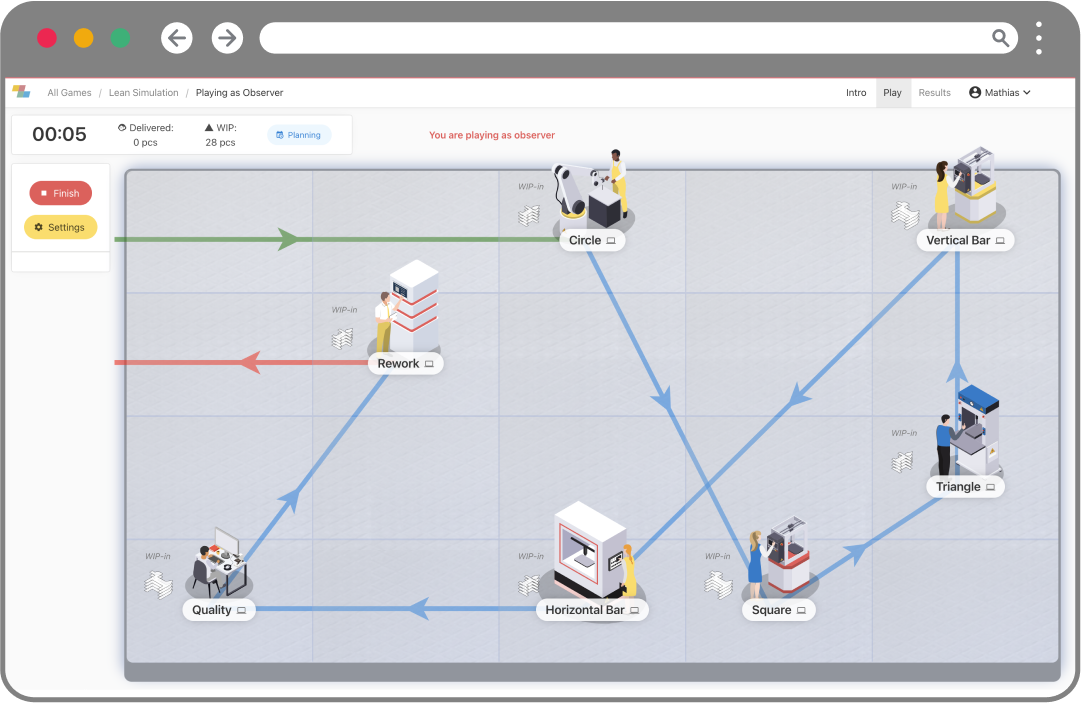
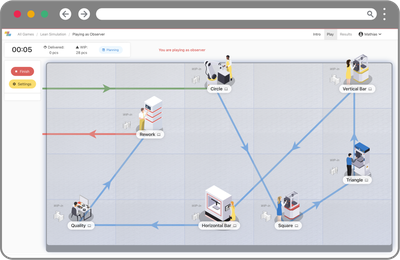